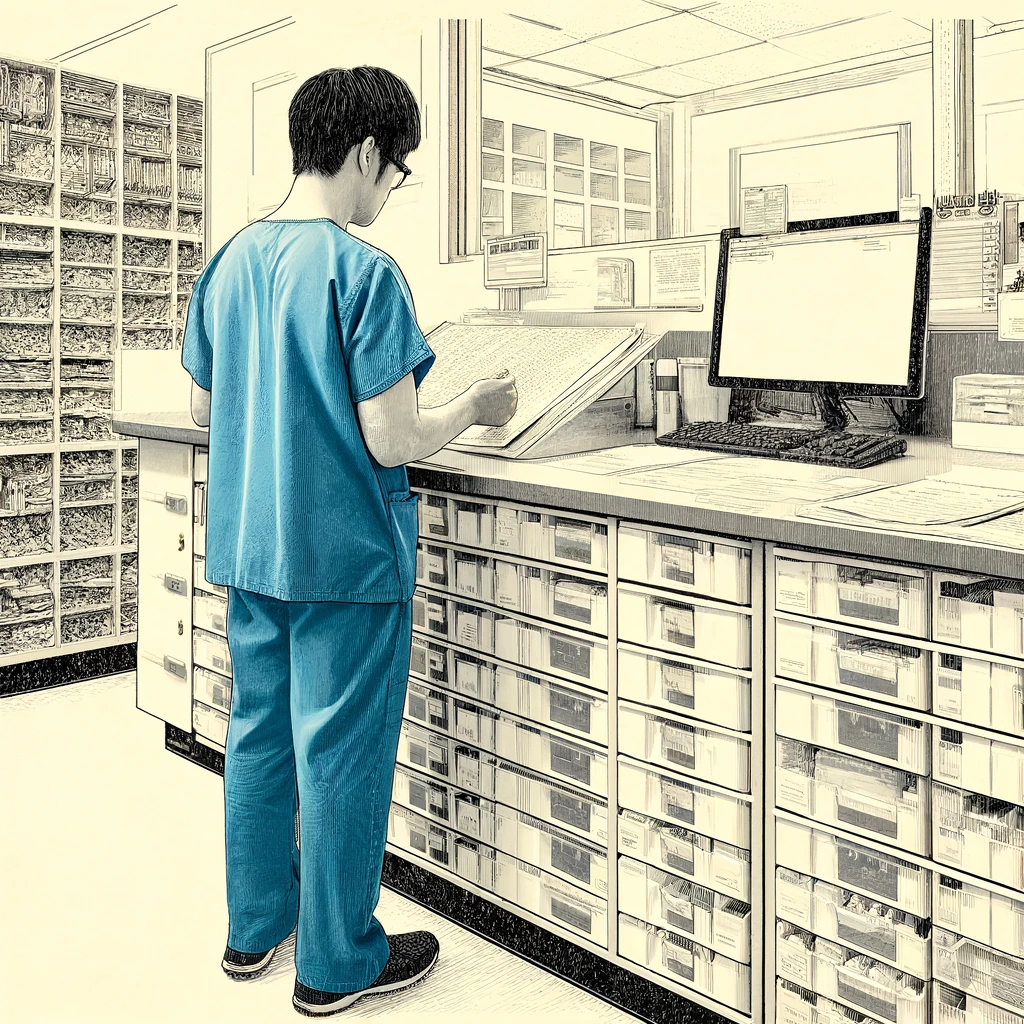
Wherever medications are compounded, maintaining the highest standards of safety and quality is paramount. To achieve this, pharmacy teams must diligently adhere to purposefully crafted Standard Operating Procedures (SOPs) and rigorous documentation protocols. With the updated 2023 USP chapter, it is critical that your facility update its SOPs to ensure documentation is provided to outline how compliance is being addressed.
Standard Operating Procedures:
SOPs are not just guidelines but a commitment to excellence, reviewed annually and communicated across all staff levels. Here’s a breakdown of key SOP areas.
Garbing and Hand Hygiene:
Ensuring all staff are properly outfitted and practice stringent hygiene to maintain a sterile environment. The purpose is to maintain a sterile compounding environment, proper garbing and stringent hand hygiene are critical. SOPs for garbing detail the type of clothing, masks, caps, and shoe covers that staff must wear, and the order in which these items should be donned. Hand hygiene procedures specify the washing techniques, the type of soap or sanitizer to be used, and the length of time for handwashing to ensure that all microbial contaminants are effectively removed.
Sterilization/Depyrogenation:
Regularly verifying the efficacy of our sterilization processes (where applicable).
Component Receipt and Handling:
Careful management of components from receipt through to usage.
Cleaning and Disinfection Records:
Detailed logs of cleaning, disinfecting, and sporicidal applications to ensure consistent sanitation. To maintain a controlled environment, cleaning and disinfection are vital. SOPs for cleaning and disinfection outline the frequency and methods for cleaning different areas of the pharmacy, including cleanrooms and equipment. They also specify the types of cleaning agents and disinfectants to be used, along with their concentration and contact time required to be effective.
Documentation:
To back our SOPs, we maintain comprehensive documentation that supports our operational integrity.
Personnel Training and Competency:
Detailed records of staff training sessions, skills assessments, and qualifications are kept to ensure that all team members are competent to perform their assigned tasks. This documentation helps in both compliance and in identifying areas where additional training may be necessary.
Certification Reports and Smoke Studies:
Certification reports document the validation of cleanrooms and other controlled environments. Smoke studies visually demonstrate airflow and help identify turbulence that could introduce contaminants into sterile areas. These documents are crucial for proving that our facilities meet regulatory standards.
Environmental Monitoring:
Regular monitoring of the air and surfaces within the compounding areas is documented to detect and address any potential contamination swiftly. This includes the use of air samplers, settling plates, and contact plates to monitor levels of particulates and microbial contamination. Equipment and Compounding Records: From machinery maintenance to detailed compounding logs, all activities are thoroughly documented.
Equipment and Compounding Records:
Maintenance logs for equipment ensure that all machinery is functioning correctly and up to standard, which is vital for both safety and efficacy in compounding. Detailed compounding records track the batch number, date of production, ingredients used, and the technician responsible for each compounded formulation, aiding in maintaining high-quality outputs and facilitating recalls if necessary.
These practices ensure that every process at your facility is not only compliant but also exemplary in its execution. By committing to such rigorous standards, patients can receive the quality care they deserve.
Reach out for more insights into how we uphold our standards of excellence at TerluminaRx!
#Healthcare #Pharmacy #SOPs #PatientSafety #QualityAssurance